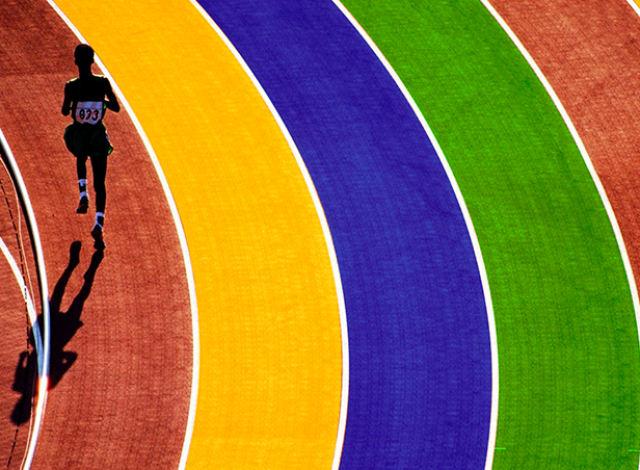
Plastic is a synthetic (or natural) polymer with a relative density of around 1g/cm3, which is only 1/4 of the relative density of iron oxide pigments. However, its resistance to deformation is moderate, between fibers and rubber, and is composed of synthetic resins and additives such as fillers, plasticizers, stabilizers, lubricants, pigments, and fillers. Plastic products are a general term for household, industrial, and other products that are processed using plastic as the main raw material. Its processing methods include injection molding, vacuum forming, blow molding, wire drawing, extrusion, 3D printing and all other processes using plastic as raw material. They have the characteristics of light weight, corrosion resistance, friction resistance, high mechanical properties, good electrical insulation, easy processing, and beauty, and can be used as structural materials, insulation materials, and corrosion-resistant materials. It is not only a necessity in people's daily lives, but also widely used in various sectors of the national economy, military industry, and cutting-edge science and technology. It can replace glass, ceramics, wood, metal, and fiber, and is an important material for industries such as airplanes, automobiles, ships, motors, machinery, chemicals, construction, and daily necessities. In order to give plastics and plastic products beautiful colors and easy identification, it is usually achieved by adding a certain proportion of coloring pigments, among which iron oxide pigment is one of the selected coloring pigments. Therefore, plastics and plastic products have also become one of the six major application areas of iron oxide pigment
5.5.1 Operation of China's plastic products industry in 2021
5.5.1.1 Growth in Plastic Product Production China is a major producer of plastic products, and in recent years, China's plastic product production has fluctuated slightly. In 2021, the production of plastic products reached 80.04 million tons, a year-on-year increase of 5.9%.
5.5.1.2 Product Industry Concentration: The plastic product industry in East China is mainly concentrated in the East and South China regions. In 2021, the production of plastic products in East China was 36.9626 million tons, accounting for 46.2% of the total production. The production of plastic products in South China accounts for 20.4%. The proportion of plastic product production in Central China and Southwest China exceeds 10%, accounting for 12.6% and 10.9% respectively. The production of plastic products in North China, Northwest China, and Northeast China is relatively small.
5.5.1.3. Expansion of China's Plastic Product Export Scale In terms of China's plastic product exports, the import volume is relatively small, the dependence on imports is low, and the export volume maintains a growth trend. The export value of plastic products in 2021 was 98.99 billion US dollars, a year-on-year increase of 29.1%.
5.5.1.4. Plastic product enterprises continue to increase their production of plastic products in China, and the number of related enterprises is also increasing year by year. The registered number of plastic product related enterprises was 231000 in 2016, approaching 500000 in 2019, and 1.1075 million new plastic product related enterprises were added in 2021. According to incomplete statistics, the registered number of plastic product related enterprises in operation/existence in China is 4.3572 million.
5.5.2 Characteristics of the Plastic and Plastic Products Industry The characteristics of plastics and plastic products are: light weight, chemical stability, good impact resistance, good transparency and wear resistance, good insulation, low thermal conductivity, excellent formability, good coloring, and low processing costs; But it has poor heat resistance, high thermal expansion rate, easy combustion, poor dimensional stability, and is prone to deformation; Many plastics have poor low-temperature resistance, become brittle at low temperatures, and are prone to aging.
5.5.2.1 Classification and varieties of plastics and plastic products
5.5.2.1.1 Classification of plastics based on their performance after heating
1. Thermosetting plastics are characterized by curing at a certain temperature for a certain period of time after heating or adding curing agents. The cured plastic has a hard texture and is insoluble in any solvent, and cannot be softened again by heating. If the heating temperature is too high, it will decompose. Common thermosetting plastics include bakelite, electric jade, decorative panels, phenolic and unsaturated polyester plastics, etc. 2. Thermoplastic plastics are characterized by softening upon heating, hardening upon cooling, and generally maintaining their chemical properties only through physical changes during processing. The resin of this type of plastic is mostly polymerized. Common thermoplastic materials include: nitrocellulose plastic, acetate fiber plastic, polyethylene plastic, polypropylene plastic, polystyrene plastic, polyvinyl chloride plastic, etc. For example, common mineral water bottles, plastic bags, etc.
Classified by application scope
1. General plastics This type of plastic mainly refers to a type of plastic with large production, wide applications, and low prices. They account for about 80% of the total plastic production. The main varieties include polyethylene, polyvinyl chloride, polypropylene, polystyrene, phenolic and amino plastics, etc.
2. Engineering plastics generally refer to plastics that can be used as structural materials in engineering technology. The significant characteristics of this type of plastic are high mechanical strength, strong resistance to chemical corrosion and high temperature, and can replace metals or be used for other special purposes. The main varieties include polyamide, polycarbonate, polyoxymethylene, polysulfone, ABS, polyphenylene ether, fluoroplastics, etc. Classified by flammability level: 1. Flammable plastics. This type of plastic burns violently when exposed to an open flame and is not easily extinguished. Such plastics as nitrocellulose plastics are classified as hazardous materials.
2. Combustible plastics: These types of plastics burn when exposed to an open flame and have no self extinguishing properties, but burn quickly. Such as polyethylene, polypropylene, etc.
3. Non combustible plastics can burn in strong open flames and quickly extinguish after leaving the flame. Such as phenolic plastics, acetate fiber plastics, polyvinyl chloride plastics, etc. In order to improve the performance of plastics, various auxiliary materials such as fillers, plasticizers, lubricants, stabilizers, modifiers, colorants, etc. are usually added to the resin to make plastic products with good performance. The so-called modified plastics refer to the use of physical, chemical, or a combination of physical and chemical methods to achieve expected changes in the properties of plastic materials or to endow them with new functions, resulting in completely new materials. The modification process is sometimes carried out during plastic polymerization, while more often it is carried out during the processing of plastic products. The means to achieve plastic modification include filling, blending, and reinforcement.
5.5.2.1.2 Types of plastics
5.5.2.1.2.1 Thermoplastic Varieties The molecular structure of resin in thermoplastic is generally composed of one or more "basic units" arranged in a certain way, repeatedly connected by chemical bonds, like pearl chains, in a linear or branched structure, often referred to as linear polymers. The main varieties and properties of thermoplastic plastics are as follows. 1. Polyvinyl chloride (PVC), also known as polyvinyl chloride, is a thermoplastic resin made by polymerizing vinyl chloride monomer. It is one of the main general-purpose plastic varieties and ranks second in production capacity among the world's top five plastics, after polyethylene, accounting for about 16% of the total synthetic resin. Hard polyvinyl chloride (PVC-P) can be used to make containers (non pressure resistant), pipes, boards, wires and cables, etc. Adding a large amount of CaCO3 to make calcium plastic can increase the hardness of the plastic and replace steel or wood in making plastic doors, windows, floors, ceilings, and wire conduits. Flexible polyvinyl chloride (PVC-U) can be used to make outer packaging and film products for beverages, pharmaceuticals, and cosmetics, and is commonly used to manufacture toys, sandals, and synthetic leather. 2. Polyolefin (PO) is a polymer that contains only carbon and hydrogen elements in its molecules. The most commonly used are polyethylene and polypropylene, which are the plastics with the highest production and usage. a. Polyethylene (PE) is composed of homopolymers of ethylene and copolymers of ethylene and olefins. Polyethylene is a wax like crystalline thermoplastic resin that is odorless, tasteless, and non-toxic, with excellent low temperature resistance, stable chemical properties, and resistance to most acids, bases, and salts. At room temperature, it is insoluble in general solvents, has low water absorption, excellent electrical insulation performance, and moderate mechanical properties. However, its heat resistance, aging resistance, and environmental stress cracking resistance are poor. Polyethylene accounts for over 30% of the total plastic production and is one of the largest general-purpose plastic products. Low density polyethylene (LDPE) is a homopolymer of ethylene, also known as high-pressure polyethylene due to its polymerization under high pressure. In addition to the general properties of PE, LDPE has a low melting point, excellent heat sealing properties, and superior transparency, flexibility, adhesion, and electrical properties (high-frequency insulation) compared to HDPE. Especially, LDPE has good processability, which is why it is widely used and irreplaceable. But its mechanical properties, heat resistance, and aging resistance are slightly inferior. The main uses of LDPE are as follows: due to its high transparency, glossiness, and softness, LDPE is suitable for packaging films with high requirements, such as textiles, clothing, and food packaging. It is also used for various agricultural films to increase crop yields due to its excellent transparency; Due to its low melting point, excellent adhesion, heat sealing, and film-forming properties, LDPE can be used as an adhesive layer for extrusion coatings or composite films, and is widely used in the packaging field; Due to the fact that LDPE polymerization does not contain residual metal components of catalysts, it has high insulation properties and can be used as insulation material for power cables up to 340kV after cross-linking and high temperature resistance; Due to its excellent fluidity, LDPE can be used for injection molding various complex shaped daily necessities (bottle caps, plastic flowers, sealed containers, kitchen supplies), toys, and stationery. High density polyethylene (HDPE) is a homopolymer of ethylene with a molecular weight of (4~300000) and a copolymer of ethylene and a small amount of olefins. Due to its polymerization under normal pressure and low pressure, it is also known as low-pressure polyethylene. HDPE is a tasteless, odorless, and non-toxic white powder or milky white waxy particle. It is not easily brittle at low temperatures and has ideal oil resistance, solvent resistance, and water vapor barrier properties. However, its transparency, electrical insulation, processability, heat sealing, and bonding strength are not as good as LDPE. Compared with general plastics, polypropylene has better toughness, low temperature resistance, and aging resistance, and has better processability and operating temperature than polyvinyl chloride. The main uses of HDPE are as follows: hollow blow molded containers, packaging containers for cosmetics and oil products; Gas pipes, pressure water pipes, pipes for transporting oil and mining liquids; Injection molded turnover boxes, pallets, etc; Used as a geomembrane for anti-seepage and pollution prevention. Linear low-density polyethylene (LLDPE) is a copolymer of ethylene and 5% to 20% olefins, known as the "third-generation polyethylene" after LDPE and HDPE. Based on its structure and density, the performance of LLDPE is between LDPE and HDPE. However, due to its narrow molecular weight distribution, large proportion of medium and high molecular weight, high degree of molecular folding and winding, large intermolecular forces, and low shear sensitivity, LLDPE has its unique physical, mechanical, and processing properties. Therefore, during the molding process, the melt viscosity is high (100% to 150% higher than LDPE), the extrusion power and energy consumption are high (20% to 120% higher than LDPE), and the back pressure is also high, resulting in low output. LLDPE is the most rapidly developing resin among polyethylene resins. Its main uses are as follows: LLDPE, due to its excellent mechanical properties, can produce ultra-thin films, mainly used for films that do not require transparency, such as ice packs, frozen food packaging films, and garbage bags. b. Polypropylene (PP for short). PP is a polymer of propylene monomer under certain temperature and pressure. The density is only 0.9-0.91g/cm3, making it the smallest relative density variety among general plastics. It is non-toxic, odorless, and has good heat resistance. It can be used for a long time at around 110 ℃. PP can be processed into films, fibers, hollow containers, and injection molded products using extrusion, injection molding, and blow molding methods. Due to the presence of tertiary carbon atoms in the molecular chain, the hydrogen on it is easily attacked by oxygen, resulting in poor aging resistance. 3. Styrene based resin. Styrene resin is a thermoplastic resin formed by homopolymerization or copolymerization with other monomers. Styrene products range from highly transparent SAN products to high coverage ABS. Currently, styrene resin production ranks fourth only after polyethylene, polyvinyl chloride, and polypropylene. a. Polystyrene (PS), also known as general-purpose polystyrene (GPPS), has a relative density of 1.04-1.09, excellent dimensional stability, low shrinkage rate, and low moisture absorption. Therefore, it maintains dimensional stability and strength in humid environments, and does not promote bacterial growth. PS has a transparency of 88% to 92%, a refractive index of 1.59 to 1.60, a thermal deformation temperature of about 70 to 98 ℃, and a thermal conductivity that does not change with temperature, making it a good cryogenic insulation material. When the temperature exceeds 300 ℃, PS will decompose. PS has good dielectric properties and insulation. PS is widely used in the optical industry because it has good transparency and can be used to manufacture optical glass and optical instruments, as well as transparent or brightly colored items such as lampshades and lighting fixtures. PS can also produce various electrical components and instruments that work in high-frequency environments. In order to improve the brittleness of PS, people graft polystyrene onto rubber (butadiene rubber or styrene butadiene rubber) to give it both rigidity and toughness, which is called high impact polystyrene (HIPS). The impact strength of HIPS can be 3-4 times higher than that of ABS. In recent years, its development has been rapid, accounting for 60% of PS production, and the production of HIPS in many countries has exceeded that of PS and ABS. HIPS is easy to extrude and inject, and can also undergo secondary processing. HIPS can produce packaging containers such as thin cups, extruded dairy containers, etc. It can also be used as a casing for household items, educational supplies, radios, televisions, and other household appliances, as well as components for washing machines, freezers, and refrigerated trucks. b. Acrylonitrile Butadiene Styrene (ABS) resin is a copolymer of three monomers: acrylonitrile, butadiene, and styrene, exhibiting good synergy. Acrylonitrile endows it with chemical corrosion resistance, surface hardness, and thermal stability; Butadiene endows toughness; Styrene endows rigidity and processability. Thus, ABS with different performance can be produced by using three components in different proportions. ABS is an amorphous polymer material with a light ivory color appearance, opaque, non-toxic, odorless, and a relative density of about 1.05. It has good comprehensive performance and is a tough, hard, and rigid engineering plastic. The melting temperature of ABS is 217-237 ℃, and the thermal decomposition temperature is greater than 250 ℃. And its impact strength changes very little with temperature drop, and can be used for a long time at -40~100 ℃. Due to the presence of double bonds of butadiene, it has poor weather resistance, is prone to aging, discoloration, and even cracking, thereby reducing its mechanical properties. ABS is mainly used in the home appliance and automotive industries, such as the outer shell of televisions, telephones, and instruments, and the inner liner of refrigerators; Automotive components, pump impellers, etc. After surface metallization treatment, ABS can be used to produce metal substitutes and decorative parts. c. Polymethyl methacrylate (PMMA), also known as acrylic or organic glass, is an amorphous plastic material. PMMA is lightweight, tough and transparent, with good gloss. The transmittance of visible light and ultraviolet light is as high as 92% and 75%, respectively. And glass is only 85% and 10%. PMMA has good dielectric properties, excellent weather resistance, good dimensional stability, and stable chemical properties. Its mechanical strength is more than 10 times that of ordinary silica glass. PMMA is mainly used for instrument parts, window glass, optical lenses, transparent models, car lamp covers, signal light equipment, instrument panels, blood storage containers, DVDs, light diffusers, beverage cups, stationery, etc. 4. Polyamide, polycarbonate, polyethylene terephthalate, and polyoxymethylene (POM). This type of plastic can be used as structural materials and is also known as engineering plastics. Engineering plastics are high-performance materials that can withstand mechanical stress over a wide temperature range and are used in harsh chemical and physical environments. It has good mechanical properties and dimensional stability, and can maintain its excellent performance at high and low temperatures. It has become the fastest growing material in the development of the plastic industry in the world today. a. Polyamide (abbreviated as PA, commonly known as nylon). PA is a polymer with repeated amide groups on the main chain, which is obtained by condensation of diacids and diamines or self polymerization of lactam molecules. There are many varieties of polyamide, mainly including nylon 6, nylon 66, nylon 610, nylon 1010, etc. The more carbon atoms in polymer molecules, the softer they are. Nylon 66 can be used as a board brush and shoe brush, while nylon 1010 can be used as a toothbrush. Nylon 6 and nylon 66 are widely used due to their high price, performance, and processability. The main characteristics of nylon are excellent mechanical properties, easy coloring, and non toxicity. Nylon is a flame-retardant material with self extinguishing properties. Due to its excellent comprehensive properties, nylon became the earliest engineering plastic, accounting for one-third of the total production of engineering plastics. Nylon can be processed using various methods such as injection molding, extrusion, casting, and rotational molding. As an engineering plastic, nylon is mainly used to make wear-resistant and stress resistant transmission components, and has been widely used in machinery, transportation, instrumentation, electrical, electronic, communication, chemical, medical equipment, and daily necessities. Its specific applications include gears, pulleys, turbines, bearings, pump impellers, fan blades, sealing rings, oil storage containers, etc. b. Polyethylene terephthalate (PET), commonly known as polyester. Polyester is an important variety of synthetic fibers, which is a high polymer PET made from purified terephthalic acid (PTA), dimethyl terephthalate (DMT), and ethylene glycol (EG) through esterification, ester exchange, and condensation reactions. The fibers are produced through spinning and post-treatment. Polyester has a wide range of applications and is widely used in the manufacturing of clothing and industrial products. Polyester has excellent shaping performance. After shaping, polyester yarn or fabric has a flat and fluffy shape, which can remain unchanged after multiple washes during use. PET has excellent optical properties and weather resistance, and amorphous PET has good optical transparency. In addition, PET has excellent wear resistance, dimensional stability, and electrical insulation properties. PET bottles have the characteristics of high strength, good transparency, non toxicity, impermeability, light weight, and high production efficiency. They are widely used in carbonated beverage bottles and edible oil bottles. PET can also be used in the automotive industry (structural components such as reflector boxes, electrical components such as headlights, reflectors, etc.), electrical components (engine housings, relays, switches, microwave oven internal components, etc.), industrial applications (pump housings, hand tools, etc.), and other fields. c. Polybutylene terephthalate (PBT) has a similar molecular chain structure to PET, and most of its properties are the same. However, the main chain of the molecule has changed from two methylene groups to four, making it more flexible and having better processability. PBT is one of the toughest engineering plastics. It is a semi crystalline material with excellent chemical stability, mechanical strength, and electrical insulation properties. Typical application scope of PBT: household appliances (food processing blades, vacuum cleaner components, electric fans, hair dryer housings, coffee utensils, etc.), electrical components (switches, motor housings, fuse boxes, computer keyboard keys, etc.), automotive industry (radiator grilles, car body panels, wheel covers, door and window components, etc.). d. Polycarbonate (PC) has high impact strength, good dimensional stability, colorless transparency, good coloring properties, good electrical insulation, corrosion resistance, and wear resistance. However, it has poor self-lubricating properties, a tendency towards stress cracking, high temperature hydrolysis, and poor compatibility with other resins. Polycarbonate is an amorphous material with good thermal stability, a wide range of molding temperatures, poor flowability, and low moisture absorption. However, it is sensitive to water and requires drying treatment. The main applications of PC are baby bottles, drinking cups (also known as space cups), and purified water buckets. It can be repeatedly disinfected and has better transparency than PMMA. It is also suitable for making small instrument parts, insulated transparent parts, and impact resistant parts. e. Polyoxymethylene (POM) has good comprehensive properties, with low friction coefficient and good geometric stability, high strength and stiffness, low moisture absorption, but poor thermal stability, easy combustion, and aging when exposed to sunlight in the atmosphere. Suitable for producing anti friction, wear-resistant, transmission parts, and chemical instrument parts. Due to its high temperature resistance, it is used for pipeline components (valves, pump housings). 5.5.2.1.2.2 Types of Thermosetting Plastics Thermosetting plastics have better heat resistance than thermoplastic plastics. Commonly used phenolic resins, amino resins, unsaturated polyester resins, etc. all belong to thermosetting plastics. Thermosetting plastics are commonly used in compression molding processes, and injection molding processes can also be used at temperatures between 150-190 ℃. 1. Phenolic resin (PF), commonly known as electric wood powder, is the world's earliest industrialized synthetic plastic. High mechanical strength, toughness and wear resistance, stable size, corrosion resistance, excellent electrical insulation performance, suitable for producing insulation structural components for electrical appliances and instruments. 2. Amino resin (MF, UF for short) refers to a thermosetting resin formed by the reaction of compounds containing amino or acyl amino groups with formaldehyde. At present, the amino resins widely used in industry include urea formaldehyde resin and melamine resin. Amino resin is non-toxic, odorless, hard, scratch resistant, colorless, semi transparent, and can be used to make various brightly colored plastic products. It is also widely used in aviation, electrical appliances, and other fields. 3. Polyurethane (PU for short) is the abbreviation for polyurethane, which is a general term for macromolecular compounds containing repeated amino ester groups on the main chain. It is formed by the polymerization of organic diisobydroesters or polyisohydroesters with dihydroxy or polyhydroxy compounds. Polyurethane is an emerging organic polymer material, known as the "fifth largest plastic". Rigid polyurethane foam is mainly used for building thermal insulation materials, thermal insulation materials (thermal insulation of pipeline facilities, etc.), articles for daily use (bedding materials of beds, sofas, etc., thermal insulation layers of refrigerators, air conditioners, etc., and core materials of surfboards, etc.), and transportation tools (cushion, ceiling, etc. of automobiles, planes, and railway vehicles). Polyurethane elastomers have excellent tensile strength, tear strength, impact resistance, wear resistance, weather resistance, hydrolysis resistance, oil resistance, etc. Mainly used for coating materials (such as hoses, gaskets, tires, gears, pipes, etc.), insulators, shoe soles, and solid tires.
5.5.3. The coloring processing technology and requirements for plastics and plastic products. Plastic coloring is a system that is related to the application objects, application formulas, application process methods, and requirements for coloring pigments in the application places. Therefore, it is not enough for coloring pigments to only impart various colors to plastics. They also need to meet the various process conditions in plastic processing and have good application performance under usage conditions. The basic properties that plastic coloring agents should possess include color performance, coloring power, covering power, and dispersibility; Heat resistance, light resistance, weather resistance, migration resistance, acid resistance, alkali resistance, solvent resistance, and chemical resistance; The processability and safety of shrinkage and warping. The various properties of coloring pigments are not only closely related to their chemical structure, but also to their crystal form, particle size, particle distribution, concentration, and conditions of use. Coloring is also related to the type of plastic and plastic additives, especially to the processing technology of plastic products.
5.5.3.1 Processing techniques for coloring plastics and plastic products: There are three processing techniques: direct coloring method, coloring agent method, and full-color modified material method. 1. The direct coloring method is to directly add pigment powder to resin, stir and mix it, and synchronously color and shape it. Its advantages include simple process, low cost, no compatibility issues, and no impact on the physical properties of the product. Its disadvantages include: easy generation of dust flying, serious cross pollution caused by production equipment, site and environmental pollution, difficulty in changing colors and varieties, and high requirements for pigment dispersion. 2. The coloring agent method involves preparing high pigment content color masterbatch, pre dispersed pigment, color paste, color paste, color sand, and 3D printing filamentous plastic additives. Plastic product manufacturers only need to purchase plastic coloring agents that match the main resin before coloring the products. Its advantages include shortening the transportation cycle of natural plastic, low storage costs, providing supply and storage of natural plastic in containers or bulk form, reducing the amount of waste from coloring agents, and providing high flexibility in color matching. Manufacturers of coloring agents can provide and serve new coloring agents more quickly. Disadvantages: Additional equipment is required, stricter training for operators, and higher requirements for quality assurance. 1. The full-color modified material method is to simultaneously add the process of directly coloring with pigment powder in the plastic mixing modification process, so that the modified coloring is completed synchronously. Its advantages: good overall uniformity, no need for dilution during the molding process. Its disadvantages include difficulty in changing colors and varieties, and higher requirements for pigment dispersibility.
5.5.3.2 Production and processing technology of plastic products The processing technology of plastic products includes compression molding (compression molding), extrusion molding (extrusion molding), injection molding (injection molding), blow molding (hollow molding), rolling and 3D printing, etc. The components of plastics include synthetic resins, fillers, plasticizers, stabilizers, colorants, lubricants, antioxidants, anti-static agents, etc.
5.5.3.3 Requirements for heat resistance of coloring pigments in the processing technology of plastic products The biggest difference between plastic coloring and coloring of other materials such as coatings, cement, and paper products is that the vast majority of plastic coloring and molding involve a heating process. In the early development of the plastic industry, processing temperatures above 200 ℃ were rare. But now processing temperatures of 300 ℃ or even higher are also very common. The processing temperature range of various plastics is different from each other. Colored pigments often undergo decomposition and color changes when heated during plastic molding, which can also affect their light resistance and mobility. Therefore, heat resistance is a very important indicator in plastic coloring. The so-called heat resistance refers to the temperature at which there is no significant change in color, coloring power, and performance at a certain processing temperature and for a certain period of time. Mastering the molding temperature of plastic products and selecting appropriate coloring pigments are particularly important.
5.5.4. Iron oxide pigments for plastics and plastic products. Iron oxide pigments have high coverage, strong coloring power, and wide color spectrum. The main colors are red, yellow, and black, and the composite colors are orange and brown. They have good dispersibility and can be mixed with various coloring agents to produce various colors. And it has excellent chemical stability and physical fastness, especially in terms of migration resistance, weather resistance, chemical corrosion resistance, water resistance, oil resistance, solvent resistance, and resistance to polluted air, which are applied to plastics. Conventional products include iron oxide red, iron oxide yellow, iron oxide black, and iron brown; Heat resistant products include zinc iron yellow and manganese iron black. Among these metal mixed iron oxides, zinc ferrite is important; Functional products include transparent iron oxide, which is used to color and coat plastic films and bottles that are sensitive to ultraviolet radiation, with iron oxide yellow coating. Especially its non toxicity, a large number of toxicity and toxicology tests have not shown that iron oxide pigments are harmful to human tissues. Iron oxide pigments produced from pure raw materials can be used for coloring food and pharmaceutical products. In general, the addition of iron oxide pigments is beneficial for the photostability of plastic products because it can produce a light shielding effect. It is one of the most cost-effective plastic color colorants in terms of performance.
5.5.4.1 Quality standards for iron oxide pigments used in plastics and plastic products. Iron oxide pigment products used for coloring plastics and plastic products shall comply with the national GB1863-2006 standard for iron oxide pigment products. Attention should also be paid to the influencing factors of the 13 plastic pigment testing standards officially implemented on December 1, 2014
5.5.5 Application of Iron Oxide Pigments in Plastics and Plastic Products 5
5.5.1. Application of Iron Oxide Red Iron oxide red is the most stable compound in iron oxide pigments, and its color varies from yellow red phase to red purple phase due to different manufacturing processes or post-processing techniques. It has excellent heat resistance, high coloring and covering power, good light resistance, weather resistance, solvent resistance, water resistance, and acid and alkali resistance.
5.5.5.2 Application of Iron Oxide Yellow The chemical formula of iron oxide yellow is Fe2O3 · H2O. Due to the presence of crystalline water, its heat-resistant temperature is: below 140/℃, it does not change color, and after dehydration at 270-300/℃, it turns red gradually, eventually turning into iron red, which affects its wide application in plastics and plastic products. Coating the surface of iron yellow pigment can make it suitable for certain high-temperature applications. The chemical composition of Zinc Iron Yellow (C.I. Pigment Yellow 119) is zinc ferrite, with a brownish yellow color. It is produced by calcination and has a heat resistance of over 300 ℃. The main properties of iron oxide yellow pigment are: it is a bright yellow color, almost equivalent to chrome yellow, with strong covering power, stable light effect, and light resistance up to level 8. Has good weather resistance. Iron oxide yellow is only suitable for coloring rubber, EVA, etc. due to its poor heat resistance. The price is relatively low and non-toxic, and it is widely used for light color and color matching. Producing composite iron phthalocyanine green by color matching with phthalocyanine blue and phthalocyanine green for the production of artificial turf and similar products.
Zinc iron yellow; Chemical composition: [ZnFe2O4], is a type of mixed metal iron oxide yellow pigment with spinel crystal form. It has stable chemical properties, good covering power, and excellent heat resistance up to 300 ℃. It can be used for coloring engineering plastics and can be used in plastic processing formulas and food contact plastics that cannot use lead or cadmium pigments. Zinc iron yellow can be mixed with iron red to obtain orange or light brown chromatography. It will not cause deformation when used in HDPE.
5.5.5.3 Application of Iron Oxide Black Pigment
Iron oxide black tetrairon oxide, divided into the formula Fe3O4 or Fe2O3 • FeO. The unique molecular structure results in poor heat resistance, with a color change at 80 ℃, a transformation to γ - Fe2O3 iron red at 200 ℃, and a transformation to α - Fe2O3 iron red above 300 ℃. Due to the widespread use of carbon black pigments, ordinary iron oxide black is not widely used in plastic coloring unless its color changing effect is utilized. Some people have also expanded its application range by using high-temperature resistant manganese iron black.
5.5.5.4. Application of Iron Oxide Brown Pigments The commonly used iron oxide brown is a composite of iron oxide black, iron oxide yellow, and iron oxide red. The presence of iron yellow and iron black has poor heat resistance and is affected in the application of plastics and plastic products. Manganese iron brown can be used to meet the needs of plastic products. Manganese iron brown pigment can be regarded as one of the variants of iron oxide red. Iron in iron oxide red is partially replaced by manganese, and the color changes from brownish red to brown. Main performance: Manganese iron brown pigment is inert, with high coloring power and strong covering power. It has excellent heat resistance, up to 300 ℃, light resistance, and good weather resistance.
5.5.5.5 Precautions for the application of iron oxide pigments in plastic coloring: 1. Iron oxide black contains divalent iron, which can be oxidized, and this process is exothermic. Therefore, the storage temperature for black and brown pigments should not exceed 80 ℃. 2. Iron oxide yellow cannot be used in combination with lead salts in polyvinyl chloride PVC, while iron oxide red can react with hydrogen chloride in polyvinyl chloride PVC, producing a compound that is a catalyst for the degradation of polyvinyl chloride. 3. It has a promoting effect on the UV aging of polyethylene PE. 4. Although iron oxide red in polypropylene PP can inhibit photo aging, it may also reduce the effectiveness of benzotriazole, benzophenone, and organic nickel salt light stabilizers in polypropylene by more than 20%.